THE FOUNDRY
The pictures below show the construction and initial learning phases of the foundry.
Click here to see later photos of the parts that have been
made.
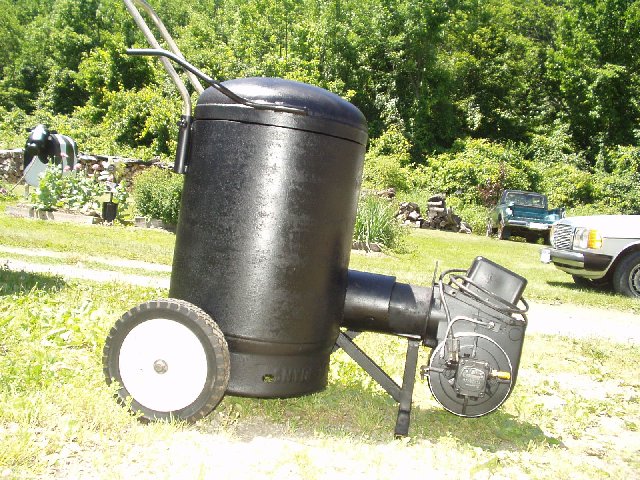
The furnace was built from a 30 gallon
propane tank that was shortened up. the interior is lined with a commercial refractory cement; several homebrew
refractories were tried and found to be more trouble than the money they saved. The furnace is fired with a conventional
oil burner gun.
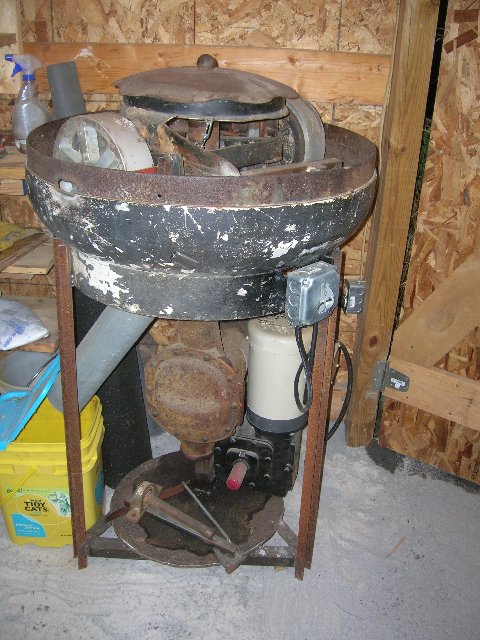
The muller. Nobody does serious casting
without a muller to mix or moisten their sand. I cannot imagine working without it.
The muller body is made from the top of a 125 gallon propane tank, cut loose and inverted as a bowl. A quarter inch plate
steel was welded in to make a flat floor for the squisher wheels to run on. The squisher wheels are machined from discarded
concrete- grinder wheels and loaded with two barbell weights. The rotating assembly... the wheels and their mounting frame... weigh
about 100 lbs.
Click here to see clearer pictures of the muller under construction.
The machine was originally powered with a 3- phase 3HP motor from the scrap yard, but we determined that a 1HP single phase motor
would work just as well and not require us to be running back and forth to the phase converter switch. The motor drives a
right angle gear reduction which chain-drives a small pickup truck rear- end. One axle was cut from it, and the other axle
protrudes through the bottom of the bowl and the floor plate. A suitably butchered tire rim is bolted to the end of the
axle and it slips over the squisher wheel assembly. It turns about 25 RPM and pulls a pair of plows behind it; one plow
scrapes the sand from the outside in, and the other moves the sand from the inside out.
Capping the unit is a cultivating disk and part of a "finial" from a wrought iron fence rail. God bless scrap dealers who
let you go "shopping!"
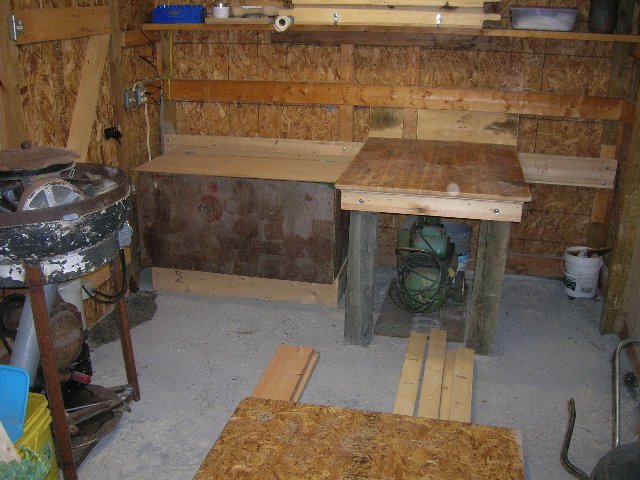
The foundry interior... which we have not
used yet! We spent four weekends learning how to make a "perfect" part, and for each of those weekends the casting
operation took over my workshop. Sand got everywhere; it was OK as a temporary fix, but unsustainable as a permanent
function.
To the left is the muller, then the insulated sand box which can be heated to keep the sand from freezing, and then the
"pounding table" for ramming up flasks. A wheezy old air compressor lives under the bench. The boards on the sandy floor are for a 10 X 10 pavilion roof for the melting and
pouring operations, although there is also provision to do that inside when the weather is really poor.

The back of the pattern faces the camera after
it has been removed from the cope and
drag. This was our first attempt at mold- making... note that the sand has never been used. Our sand is a fine "fracking"
sand that comes to the area by the trainload and moves out by the truckload... Some is always spilled, and my son got a ton
of it, bucket by bucket, from between the rails. We mix it with bentonite.
The pattern is a wheel truck for a 1/12 scale DD40 diesel locomotive. The need for this part has driven this whole foundry project.
Brian's website,
btilden.com, will be showing more and more of the train parts that he is building.
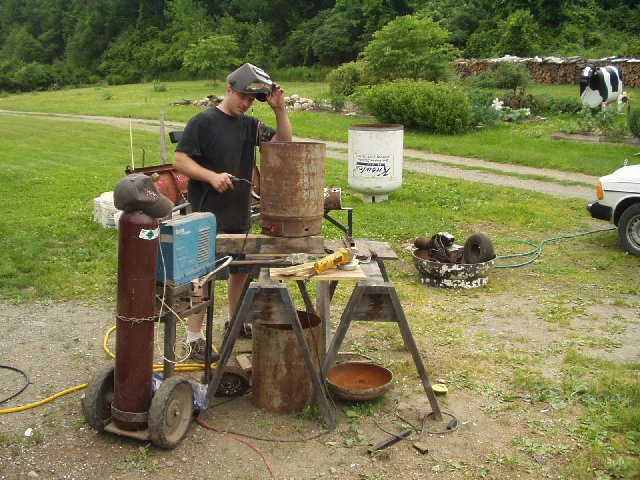
June 2010, the start of the project. Brian is
welding on the furnace body; below the table is the excluded length of the tank, and the top which was reattached with a
swivel. In the near background is the propane tank top (black, full of junk) that became the muller bowl. The remainder of
the tank became a fan-tastic burn barrel. Further in the background is my "tin cow", made from a 275 gallon oil tank, a
milk can, and some other scrap.
The welding cart is still another story. It rides on a set of Planet Junor" rototiller wheels and was specifically
designed to maneuver the welder and its large gas tank through a cluttered shop.
I also built a "breaking furnace" which melts transmission cases, engine heads, etc into ingots to feed the casting
furnace. It looks crude but runs very well. Click here to watch a You Tube video of it at work.